A New Sound System for Roy Thomson Hall
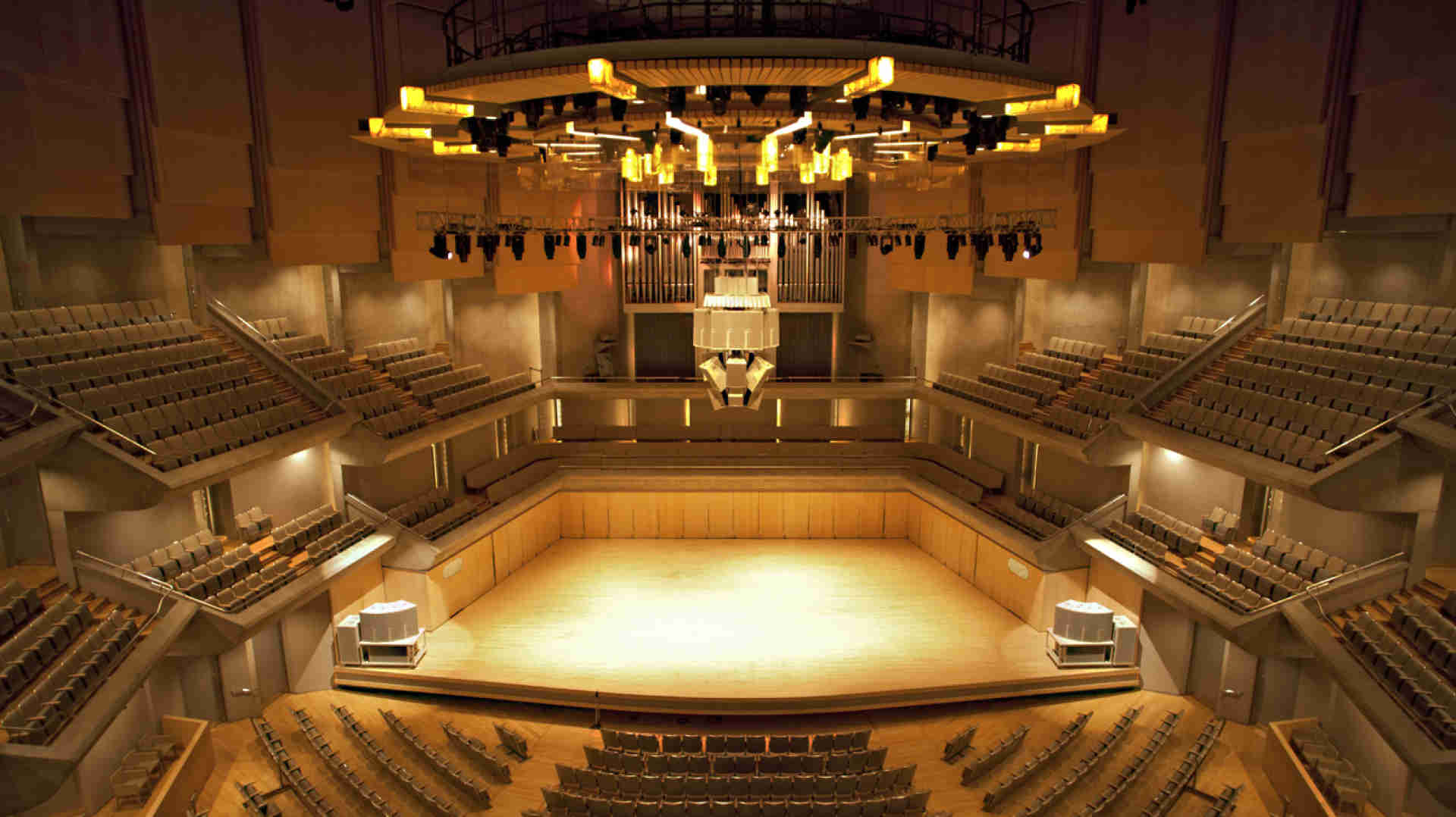
More than 25 years after the installation of its original audio systems, Toronto’s iconic 2,630-seat Roy Thomson Hall has undergone a complete renovation of its performance sound and communications systems and related infrastructure.
The renovation uncovered some unexpected surprises, and called for significant design ingenuity to fit a rather large round peg into a small square hole.
As is the case with most concert halls dedicated primarily to the performance of symphonic music, an electroacoustic performance sound system is deployable on demand at Roy Thomson Hall for popular music concerts, master classes, and other performances that supplement the schedule of the Toronto Symphony Orchestra and Toronto Mendelssohn Choir, its primary tenants.
An acoustical renovation in 2002 markedly improved the hall’s sound, which had been criticized by performers as being too cold. Along with other significant enhancements to the acoustics, the original adjustable reflective acrylic disks suspended over the stage were replaced by a single large circular wooden canopy constructed from thick, closely set wooden beams radiating from a small central ring. The existing sound-reinforcement system from the 1980s was not replaced, however; instead, it was rigged to retract through a pair of doors in the center of the new canopy.
Martin Van Dijk, partner and director of Toronto consultants Engineering Harmonics, who has been involved with Roy Thomson Hall for many years as an aficionado of the symphony, sound engineer, and consultant, knew that what he had been hearing during amplified performances just wasn’t right.
“I could hear predominant acoustic anomalies in that room, but I needed to do a proper survey to determine exactly what they were from a scientific and engineering point of view,” Van Dijk recalls.
Engineering Harmonics has designed performance sound systems for acclaimed concert halls around the world, including the Margot and Bill Winspear Opera House at the AT&T Center in Dallas, Kansas City’s Kauffman Center for the Performing Arts, and Koerner Hall in Toronto.
“We set the bar very high for what we do,” says Engineering Harmonics’ partner and director Gary Tibshirani. “In designing a sound-reinforcement system for any room that has been created to be an essentially acoustic space, it is imperative that we undertake a thorough acoustical analysis before we start down the road to design and specify a sound-reinforcement system. Our goal as consultants is to create a great marriage of acoustics and performance sound, and, like a good marriage counselor, we strive to understand the underlying issues and the tensions that exist between them, as well as those that may arise when they are driven to extremes.”
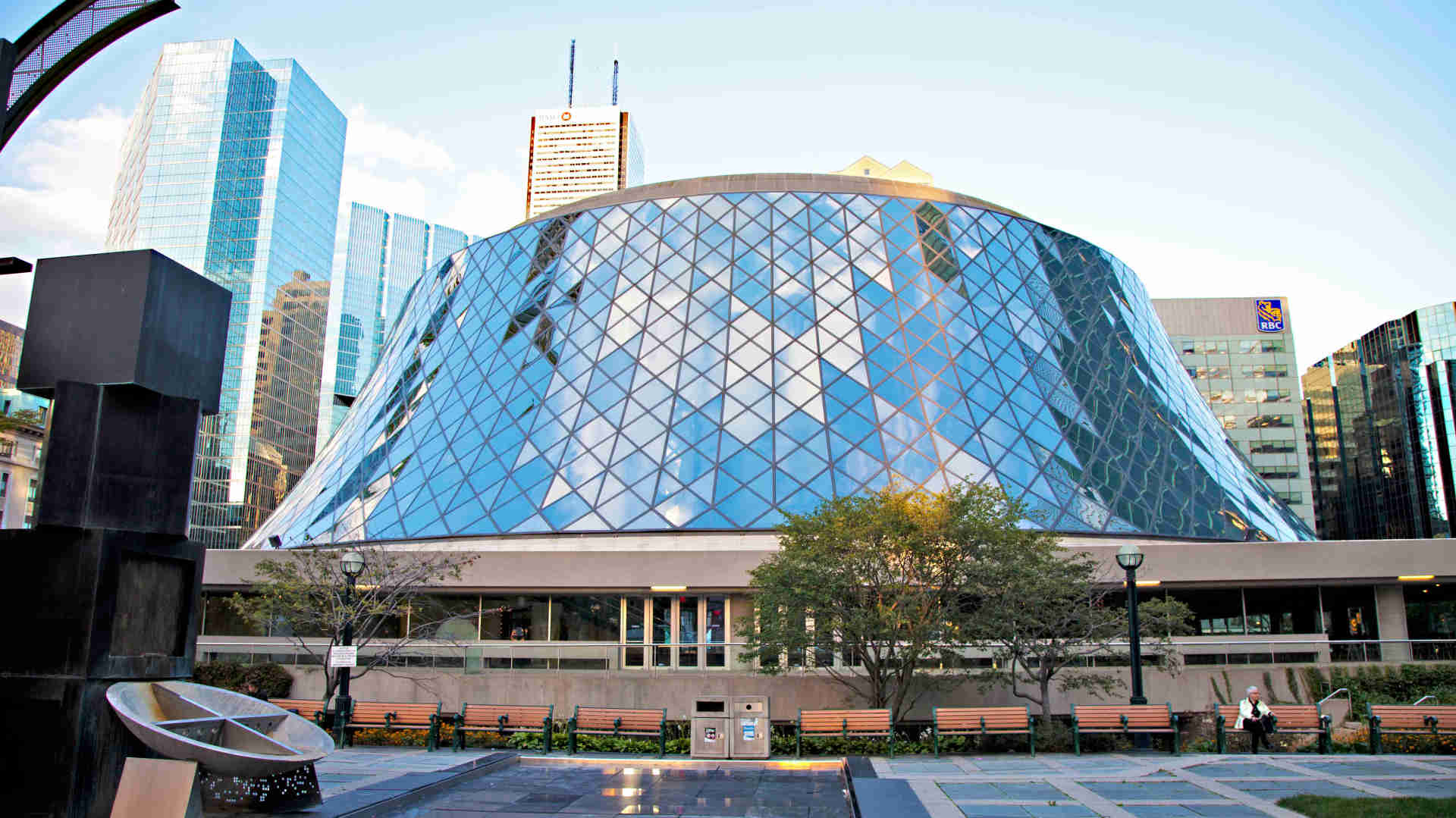
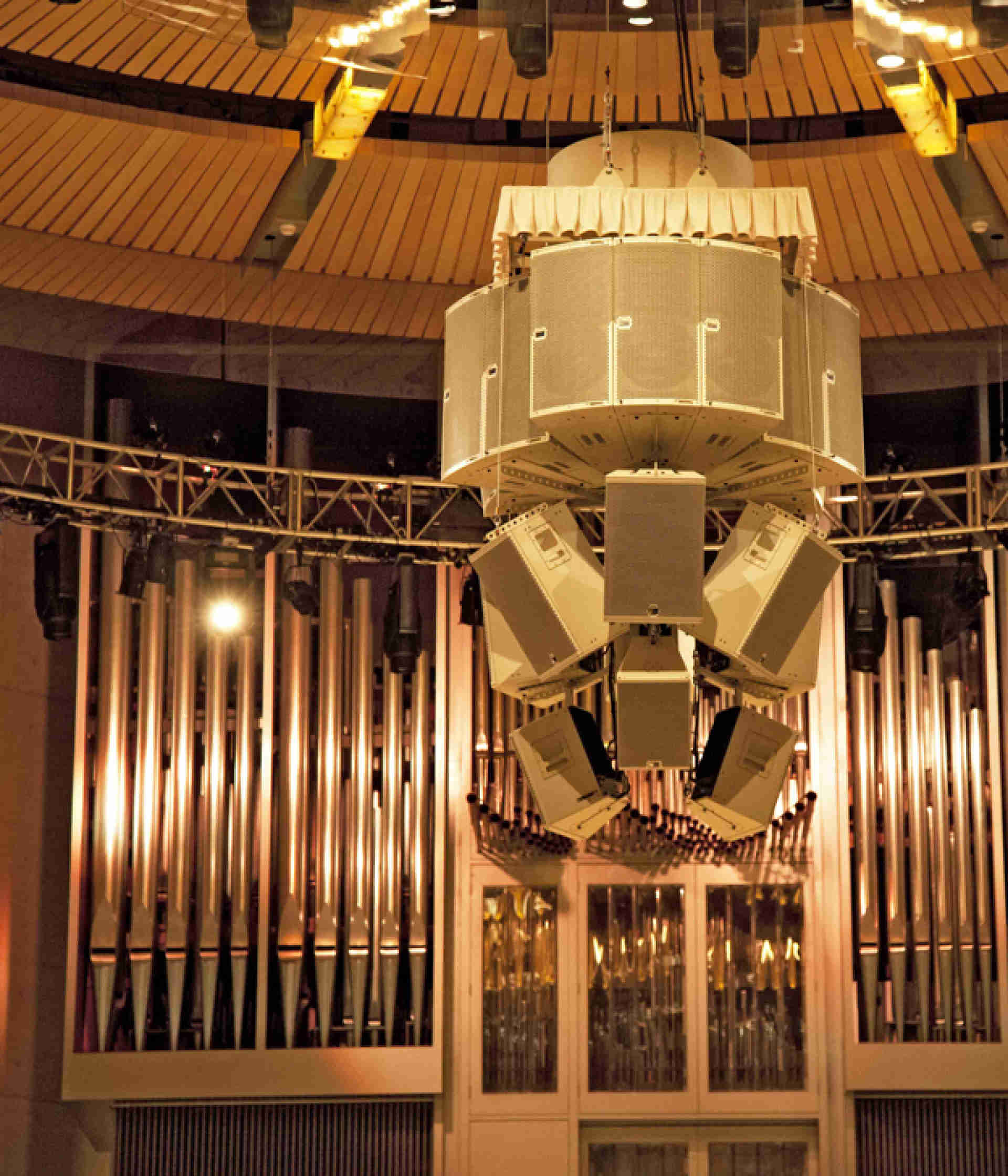
“The seating pods are arrayed very close to 20° apart, and that allowed us to create the cluster shape we needed in order to stay focused on the audience and away from the walls as we curled around the hall. By the time you wrap around to the side of the seating, you’ve already stepped an entire floor down. In other words, the side seating on the third level is at the same height as the center seats on the second level. That’s how droopy that hall gets. The fronts of the pods have a hard reflective surface on them, so you have a lot of incentive to turn and head down as you go around. That’s what the JM-1P allowed us to do, because of its tight 20° pattern.”
MCCARTHY
Enlisting the aid of Meyer Sound “scientists” to collect acoustical data, Van Dijk completed a study confirming that the acoustic anomalies in the hall were created primarily as a result of two factors: uncontrolled reflections from specific surfaces, and acoustic interference between loudspeakers in the existing system that caused cancellations at specific frequencies.
In a 2011 site assessment, Van Dijk noted that the acoustically reflective surfaces that are designed to project the sound of the orchestra from the stage into the audience areas could become a significant liability for loudspeaker systems when reflections combined with the original sound. The resulting minute echoes often led to a reduction of clarity and intelligibility of speech. These effects were much more noticeable during amplified performances, when the amplified instruments on stage were loud. As sound operators attempted to overcome the problem by increasing volume from the sound system, they created a vicious circle— the increased volume excited the surfaces even further, resulting in a battle between performers and hall acoustics.
A new loudspeaker approach
The remedy lay in replacing the existing center cluster of eight Meyer Sound UPA-1C and four Meyer Sound UM-1C cabinets. While these components represented the best available technology when the original sound system was designed in 1985, their low directivity (by today’s standards) permitted the projection of unnecessary acoustic energy onto those reflective surface areas that should have been avoided.
Their low directivity also gave rise to a heavy interference between the loudspeakers themselves. “The current loudspeaker devices were designed to be arrayed in small quantities of two to three units,” Van Dijk notes. “The current cluster exceeds the number of devices that should be organized into an array. The older loudspeaker devices interfere with each other, causing cancellations at specific frequencies. This results in reduced intelligibility, as well as the cluster’s reduced ability to reproduce tonally balanced music.”
Van Dijk and Bob McCarthy, Meyer Sound’s director of system optimization, designed a replacement center cluster based largely on the new Meyer self-powered JM-1P loudspeaker. Featuring 20° horizontal and 60° vertical coverage, the JM-1P is designed to be arrayed in configurations of multiple units.
“The staggered seating pods of Roy Thomson Hall create a really interesting pattern puzzle from the point of view of a loudspeaker,” McCarthy says. “As you move off center from one seating section to the next, the sections step down and get lower and lower. They’re a moving target. When you aim a loudspeaker horizontally, if it’s on the correct target at its center, then it will be shooting into the hostile territory of reflecting surfaces as soon as you move off the center.
“As it happens, the seating pods are arrayed very close to 20° apart, and that allowed us to create the cluster shape we needed in order to stay focused on the audience and away from the walls as we curled around the hall,” he continues. “By the time you wrap around to the side of the seating, you’ve already stepped an entire floor down. In other words, the side seating on the third level is at the same height as the center seats on the second level. That’s how droopy that hall gets. The fronts of the pods have a hard reflective surface on them, so you have a lot of incentive to turn and head down as you go around. That’s what the JM-1P allowed us to do, because of its tight 20° pattern.”
The hall’s design calls for the center cluster to be retractable through a 96″ opening in the center of the acoustic reflector suspended directly above the stage. This imposed a limit on the maximum size of the cluster design, which Van Dijk and McCarthy conceived as a seamless 220° wrap of 11 JM-1Ps, augmented by seven Meyer Sound UPQ-1P cabinets rigged below them for downfill and backfill. “I can’t believe the dice just rolled our way. Everything was looking great. Martin was happy, I was happy and, lo and behold, it would not fit through the donut hole—it was mere inches too big,” he says.
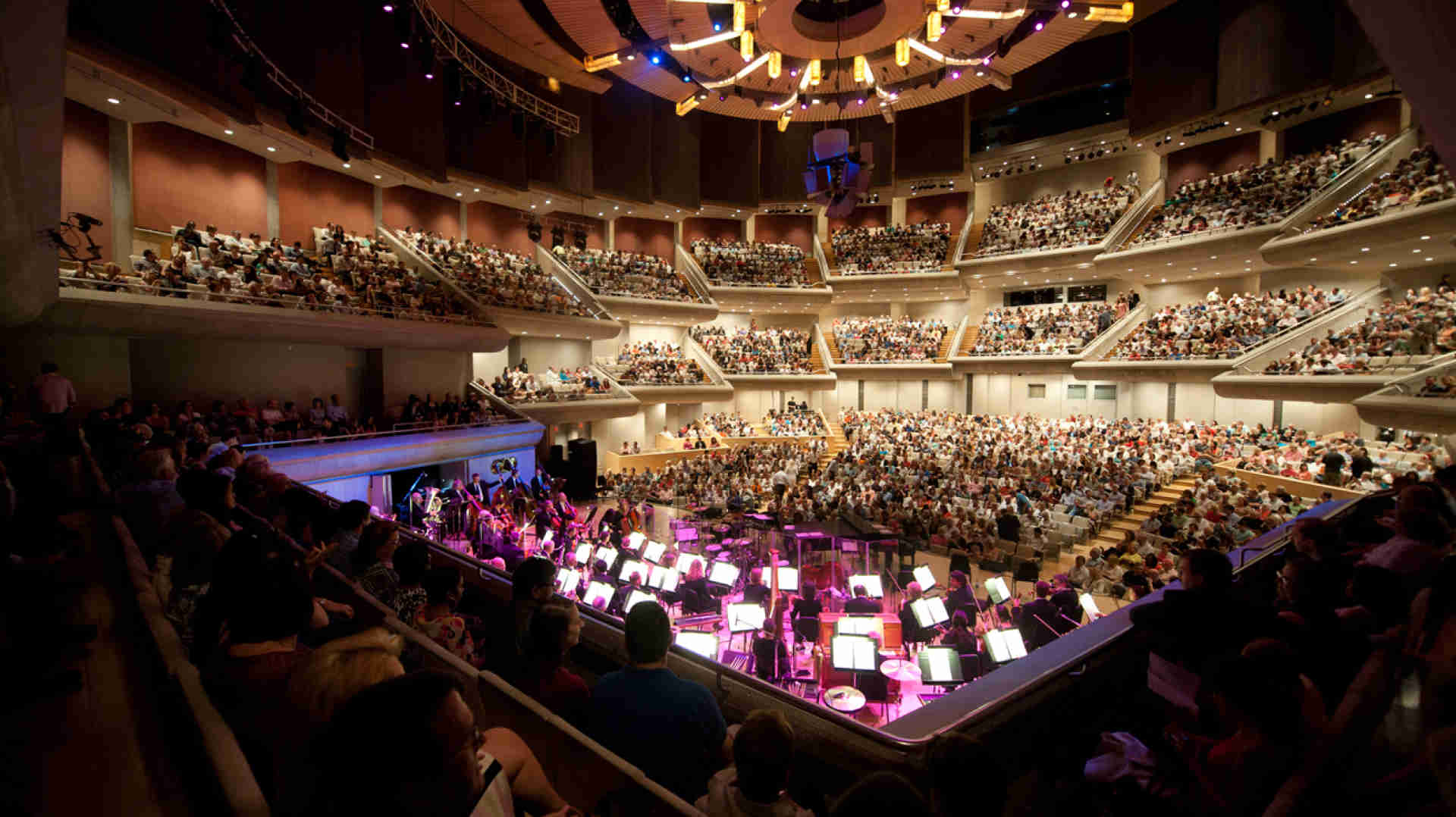
A square peg in a round hole
“In designing the cluster, we had taken the size of the opening into account from the drawings, but we found, when we went up to the canopy to inspect it, that the doors don’t operate fully open, and the full aperture is not available,” Van Dijk recalls. “Somehow, we had to find a way to squeeze the cluster into a smaller form factor.”
Working with Andy Foord, designer at project contractor and installer Westbury National Show Systems, the team redesigned the cluster through a number of successive iterations to fit the opening. Van Dijk notes, “This was a mechanical 3-D jigsaw rigging puzzle that Andy and his team approached with diligence, resulting in a great solution.”
In the final design, the cluster comprises nine JM-IPs, six UPQ-1Ps, and three UPA-1P cabinets, all arranged in three angled tiers for complete 360° coverage of the hall’s multiple seating levels. In order to fit through the opening, how ever, the wrap of JM-1Ps has been staggered: The faces of the front three share the same arc; the faces of the next pair on each side lie on an arc about 4″ toward the center point of the cluster; and the remaining cabinet toward the rear of each side is rigged a further 4″ in toward the center point, leaving about 4″ of clearance on all sides through the open doors.
“We adjusted the time delay to the front three JM-1Ps in the 0.3ms – 0.4ms range to account for the side speakers being tucked back about 4″,” McCarthy says. The geometry has been further altered in that the two side pairs are each angled downward about 7° and the single units on each side of the cluster are angled down about 12° to follow the line of staggered seating pods around the hall.
“Geppetto would be proud of this design,” McCarthy says. “It retains enough flexibility so that we were able to aim it a few degrees here and there during the tuning when we worked to sort out the real 3-D of this thing, which was quite fascinating. All of the loudspeakers were very tactically planned for their target zones, yet there was enough flexibility that, when it came to the final step of optimization, we were able to turnbuckle and move just a few parts of the structure to get everything to fall where it needed to fall.
“The result is a really fascinating puzzle that gets all the way around 360° and targets all of the vastly irregular shapes that are presented as you move around,” McCarthy continues. “We have every seat covered. The tuning proceeded in a really orderly fashion. From the top center, we wrapped all the way around and got the top row done, and then we moved down to the next level and made the next ring, and then stitched the upper ring and the middle ring together, and then mixed in the lower ring and it just came together like the pieces of the puzzle that we wanted it to be. It was tons of fun. I love a tough one.”
Replacing the original passive loudspeaker system with active units increased the load significantly, and while most of the existing loft blocks could be reused, the drum motors for the winch had to be upgraded and the winch platform reinforced to handle the heavier load.
“The ceiling structure is somewhat like the hub of a wagon wheel, and the challenge is that we’re trying to drop the cluster right through the center of the hub, which didn’t have any spot to get through,” says Doug Wildeboer, Westbury’s project manager. “Instead, we had to create a device in the structural ceiling above the reflector that would bring those loft blocks and the lines around the center hub and back down to the point where we needed them to get it to drop down through that center hole in the reflector.”
Twelve AC circuits were added for the power amplifiers in the active loudspeakers. The original Socapex cabling that had been used to transport the speaker-level signals was reused for power distribution, and a new 12-pair audio snake was installed to feed line-level signals to the individual cabinets. The basket on top of the cluster was redesigned to receive the cabling as the cluster is retracted through the opening.
In addition to the retractable center cluster, left and right stage-mounted loudspeaker systems, each consisting of four JM-1Ps and two 700-HP subs on dolly frames, can be wheeled out from storage backstage and deployed as required.
“Mixers all want a left-right system,” McCarthy says, “so you give them enough of a left-right system to be able to cover the seating area on the floor, and it’s set up to bring the image down and provide a better fill in those areas. It’s not 100% mandatory; technically, you could just about cover everything without it, but it provides some power down to the floor that all mixers are happy to have, and gives them some capability to adjust the ratio of left-right coverage to center coverage. However, once you reach the second floor level and above, as well as the wraparound behind the stage, you’re in the coverage area of the center system.”
Van Dijk explains that when the left-right stage system is deployed, certain loudspeakers in the center cluster are turned off, “to avoid overlapping cancellation. There are presets in the Meyer Galileo 616 loudspeaker management system to select various configurations. For example, the deck loudspeakers alone can be used when the venue is not sold out, since there is no point in energizing other parts of the hall when there are no patrons there.
“Similarly with the center cluster, if there’s an orchestra with a master class, for example, with people only on the orchestra level, then the bottom part of the cluster is turned on and the upper part, which addresses the balconies, is turned off using another preset. If they want to have the image down onstage, they can roll out the deck fills.”
In his site assessment, Van Dijk noted, “The rear area of the orchestra level requires small loudspeakers to fill in the sound coverage that is not directly covered by the center cluster. The current loudspeaker complement is insufficient, resulting in uneven coverage. The coverage could be improved, particularly along the sides, with a greater number of loudspeakers.”
By tripling the number of Meyer UPM-1P underbalcony loudspeakers, he not only improved the coverage, but achieved better localization of the sound source. Each loudspeaker has its own unique processing channel, so delays can be set appropriately for the output of each underbalcony loudspeaker to fall within the Haas fusion zone and integrate properly with the output from the center cluster. The target level of the system is 105dB SPL, A-weighted.
“We used an Optocore fiber optic backbone for signal transport between the front-of-house control area and the Galileo loudspeaker management system, and it’s all AES,” Van Dijk says. “We’re essentially digital right to the output of the speaker processing, where it’s converted to analog.”
Via Optocore, any channel can be routed to any device on the network, and exported as many times as required to any destination, although in practice it is used to deliver performance sound from the Yamaha PM1D front-of-house console to the Galileo processors.
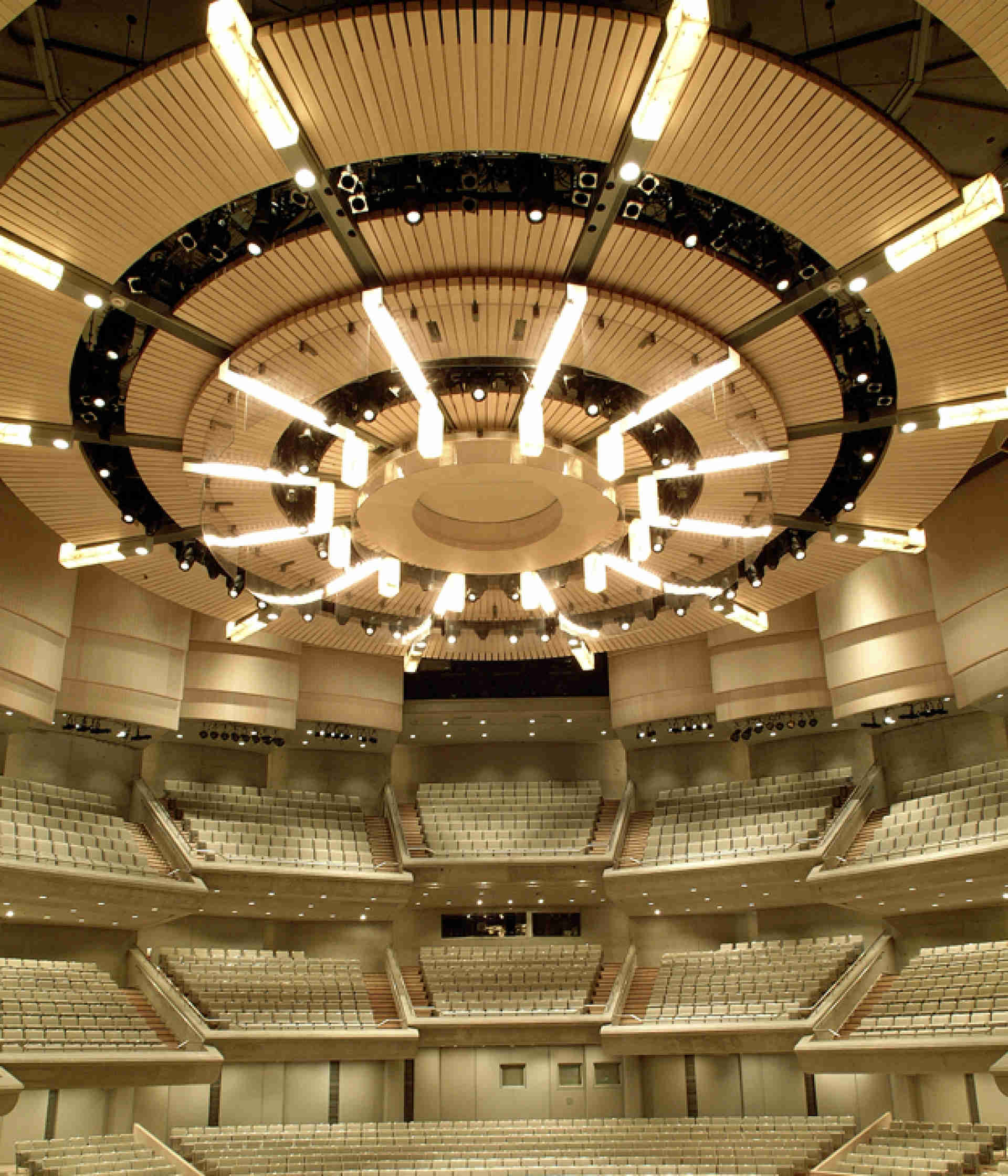
Wiring challenges
A further difficulty facing Van Dijk was that, because this was a renovation and not new construction, “detailed engineering drawings are really a waste of time, because as soon as you get on site and open up a wall to change a cable or conduit path, you may have to do a complete rework. You often don’t know what you’re going to find until you open up that part of the building and take a look.”
What they found was a number of wiring anomalies resulting from the physical renovation of the hall in 2002 when the acoustic reflector was installed over the stage. “When they did that renovation, there was an enormous amount of destruction wreaked on the original sound system signal path,” Van Dijk says. “They literally took sawzalls through conduits containing microphone lines and communications lines, which were later spliced together in junction boxes placed ad hoc throughout the area. We cleaned all that up and pulled new lines for comms and microphones.”
The original backstage and lobby paging system dated from the early 1980s, so an upgrade was included in the current renovation. The original system was, in fact, the emergency evacuation system for the hall, which under current code requirements, must be separated from the house paging system.
“They can be integrated together, but only people with the proper certification can actually touch anything, and there are virtually no AV or sound people with fire alarm certification who have the skill sets needed to manage a real sound system. It’s a very unusual skill set, and certainly the fire alarm people don’t understand the complexity of a modern sound system,” Van Dijk says. He was able to reuse most of the existing loudspeakers in the paging system, while dividing some of the larger zones into smaller areas and adding new microphones, amplification, and a Rane HAL digital distribution system that allowed him to condense two full racks of equipment down to about half a rack.
“The HAL system has a unique capability in that it can run an AES audio I/O interface 500′ on Cat 5 cable, along with serial data,” Van Dijk says, “That allowed us to deploy the very long cable lengths that were necessary in order to get audio and paging into the lobby areas. The building is essentially a concrete bunker, and finding a path for cabling out to the lobby areas that ring the hall is sometimes very difficult.”
A Crestron control system was integrated into the paging system, with touch panels backstage and in the front-ofhouse manager’s office, offering presets for control of routing, audio levels, and paging recall times in the various backstage and lobby areas.
In addition to paging, the front-of-house manager also has been given the ability to program different events in the lobby spaces. Supplementary cabling was required for permanently installed sound systems in two small adjunct performance spaces in the north and south sides of the lobby. Routing that cabling and integrating it into the whole facility presented additional challenges, and because there are only minimal spaces available to route cables to the outer ring of the circular building, cable lengths grew excessive.
When it comes to the appreciation of performance sound systems in symphony halls, expectations are usually very much like the mail – no news is good news. “If nobody says anything, that typically means it’s really good,” Van Dijk says. In this case, however, the renovation has received nothing but praise.
“The newly installed system has made an incredible difference in terms of coverage, power, and fidelity,” says Doug McKendrick, production manager for the Corporation of Massey Hall and Roy Thomson Hall. “It has been well received by both touring sound engineers and audience members alike. The quality of the equipment and install has been rock-solid for us.”